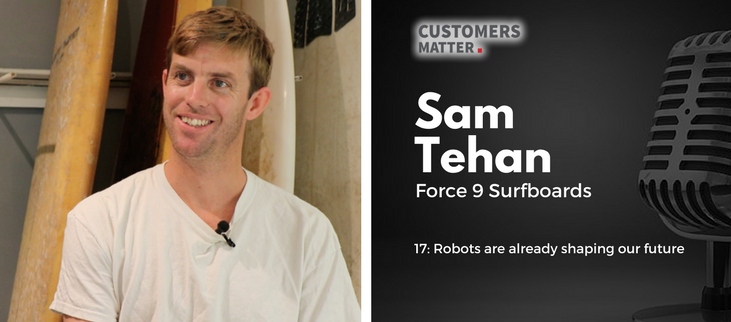
In the backstreets of Cronulla local kids are discovering something they’d never expect: “Murphy”, a robot, making surfboards.
When Murphy joined the Force 9 Surfboards team, the nature of Sam Tehan’s job was turned on its head. And while some people think robots are out to steal our jobs, Sam believes he has Murphy to thank for his job as a surfboard shaper.
John: Sam, take me back to the very beginning. I know your Dad was involved in the making of surfboards, doing the resin. How did you get involved in this industry, and what was your path into it?
Sam: Well, I started off when I was growing up, Dad used to take us to the factory he worked at. We would go in there on the weekends and we’d see all the boards getting made and see all the different custom things and individual items. The company before was a very customer-based, focused company that everything was custom-made and everything was individual. We used to hang around, pick up off-cuts and play around with those and watch these guys having fun at work and doing those things. So first job was in there, cleaning up and sweeping and fixing boards and detailing the boards and learning bits and pieces about it.
John: For people who don’t know anything about surfing or the industry, what are the basics in the shape of a board that are the big things that make a difference?
Sam: The bottom curve, like the rocker. So from nose to tail, how much curve the board has got in it. If it’s got more curve, the board will pivot and turn a lot quicker and will handle bigger waves, but it doesn’t generate a lot of speed. So a flatter board will generate a lot of speed and be a bit quicker down the line, but it doesn’t want to turn as easy. The floatation of the board, the distribution of the foam, the rails. You can start playing with everything on the board. If you put a concave in the board, then that creates lift, which can counteract with the thickness of the board and how you make it for certain individuals, to make it achieve how they surf. Because you’ll get one guy come in and he’ll lean back, the way he surfs. So if you make a board that’s too thin, the board is just going to stall. But the next guy might lean forward, the way he surfs. So that board will work unreal for him. So one guy will pick up a board and go “I don’t like this” and the next guy picks it up and goes “this is the greatest board I’ve ever had!” So it’s always a challenge of finding how a customer surfs and talking to them and finding what they really want out of a board.
John: What about the shape of the tail, the fins? What’s the significance there?
Sam: Varying your tail does change the way the board performs. A wider tail will be more slide and looser in the back; a more pintail will be a lot more drive. So you see big wave boards, they’ve got quite narrow tails, so you can get them from rail to rail pretty easy at speed. There’s a tonne of different variables in every surfboard.
John: So that makes it even more amazing that you’ve done what you’ve done. I’d love to hear this story about how you come to have a robotic arm that’s become core to your business and actually let you think more about potentially how to better meet your customers’ requirements. How did this come about? How do you come to have a robot making boards with you?
Sam: We had a sort of change in the staff here at our company, so we were looking at how to meet the demands of what we needed in the company, how do we make boards, how we make things that are other than the surfboards with the skills we’ve got. And there’s a lot of interest in the composites industry. So we’re doing a lot of composite work and sort of didn’t really realise what we were doing was composite work until we started exploring those avenues. We were like, wow, these people are doing basically what we’re doing and we’re making surfboards, not composite sandwich constructions. So we thought, how do we get to do other items? And the machines on the market, there are two or three, but they were strictly limited to making a surfboard. So if we wanted to expand out in any direction, we went we haven’t got the flexibility or the freedom to do anything other than a surfboard shape. So we started looking at what options there were out there. And pretty much we just went on YouTube and found someone using one of these robotic arms to mill a table leg. So they were following a complex curve and things that we went, we could relate that to a surfboard. And when we got down to it, we went, great, let’s see what we can do. We found someone that could some programming, that said they think they know how to get it going. So we found a second-hand one that was coming off the BMW line in Germany.
John: Hang on, just back up a bit. So you found a robot arm coming off a BMW line in Germany. How on earth did you manage that?
Sam: We pretty much just went online and started searching for used robots. There was a company there that said, we’ve got ones that haven’t done too many hours, and within our budget for what we were doing. We went, instead of spending the money on a surfboard shaping machine that we would’ve had to run flat out to make it worthwhile, let’s try something completely different and see where it goes.
John: So you found this robot that had been making BMWs. Tell me what its job had been in its previous life.
Sam: It was welding the back quarter panel of I think it’s the E63 line of BMWs. So it was probably there all day, just moving over, putting a couple of spot welds on, and then move back.
John: It was living in Germany?
Sam: It was in Germany, yes.
John: So what happened from there? How did it come to settle in Cronulla? How did you get it here?
Sam: We do a lot of consulting work for a company called Diab out of Sweden, which is one of the biggest foam manufacturers in the world. So we managed to secure a bit of shipping space in one of their containers and we got it shipped to them in Sweden. Then they moved it down to Australia for us in one of their orders.
John: You said you found a bloke who thought he could reprogram the robot.
Sam: He said he could do it.
John: Where did you find this bloke who thought he might be able to reprogram a BMW robot from Germany, to make surfboards in Cronulla?
Sam: He’s a fairly talented individual. He was studying Robotics and fairly advanced Mathematics at university. We found him through a friend of the factory. We’d just tried to design our own machines before, so we had some people that were doing work for us and doing some programming for us. But that project fell by the wayside and then we went onto to robot, and we managed to find someone that was doing this.
John: So you got this guy who studied Robotics. He came in and how did he go about reprogramming this arm? How long did it take him, and what happened?
Sam: He had no idea about surfboards; he’s not a surfer. He’s from Germany himself. He got in there and went, this is what we’ve got to do, we need to learn the program language of the robot, how we actually make a program. So we basically printed out all the manuals and started playing with the robot and went, how do we do this? We had to figure out how we wanted to board machine and how we wanted to finish off, and then we had to then relay that to him, how to make it into a surfboard.
John: The robot has got a name, I believe?
Sam: Yes. We named it Murphy. So I think Murphy was the guy in Robocop, so we figured out, Roboshaper, that was close enough for a name.
John: Tell me, you worked out how to assist Murphy through programming to make a board. How many different shapes and sizes of boards can Murphy make now, seven years later?
Sam: Pretty much anything we can design, we can machine. So there’s no limit. The limit is probably about ten foot six in length in its positioning at the moment. But other than that, pretty much as long as you’re in the working envelope, you can make a surfboard that’s a shape.
John: At the start of the interview, we discussed the different variables that go into make a surfboard. I was thinking how incredibly intricate and customised everything needs to be and how could you possibly get a robot to do so many different things? But you’re saying that in fact, you can customise infinitely within a certain square metre area?
Sam: Yes, pretty much. Yes, we can make the board, design the board, load it up, get a program off that straightaway, load it into the robot, away you go.
John: How many ways has having this robot changed the nature of what you do?
Sam: It’s definitely allowed me more time to spend on other aspects of the business.
John: Has that meant that you’ve been able to also put more time and energy into thinking about how to meet a customer’s needs?
Sam: You can sit down for a lot longer and sit with a customer and design things. If someone comes in with something that’s unique, we can actually design it up for them on the spot. They can see the board in 3D. If they want to sit there, we can actually get the board machined and we can play with it while that’s going on. And then we can go from walking in the door to maybe an hour and a half later, we’ve got your board shaped. So we can actually sit there and go, this is what you wanted to design, this is what you had in your mind, and we start turning it into that. It’s quite amazing when people go, I want to change this on my board or I want to adjust little things.
John: In terms of the number of boards Murphy has made and the efficiencies that Murphy can bring, how many boards can Murphy make in a day, if you put him to work?
Sam: You can do one about every 40, 45 minutes, and that’s not going flat out; that’s just sort of keeping everything without putting too much stress.
John: And annual leave and coffee breaks and stuff?
Sam: Loves them all! It just sits there! Whenever you walk home, turn it off, you go for a surf, it just sits there. And when you need it, you turn it on and away you go. And that’s one thing that’s helped us. So if you have a slow period or someone is away on holidays, it’s not how do we keep the work up for the rest of the staff? We can actually ride the ebbs and flows of the business. When it’s flat out, we can run 24 hours a day and punch a lot of boards out. And if we get into winter and everyone’s gone on holidays, go surfing and do those things, we can actually go, okay, we’ll calm down for a little bit.
John: Murphy, you’ve also instructed the program to do things other than just make surfboards.
Sam: Yes, we’ve done a few other parts and different things.
John: What are some of the other things that you’ve been exploring with Murphy?
Sam: The boss here, Jim, he’s into his drag bikes. So recently, we made a mould for the belly pan to catch all the oil in the bottom of the bike. The bike is also a very customised thing. It’s quite individual. So we measured it all up, made the mould, then we popped a carbon fibre belly pan that fits perfectly onto the bike. So it’s allowed us to do those things. That was a personal project. I’ve done a few table legs, done other bits and pieces for people.
John: I think you mentioned some people from the disability community even approached you?
Sam: Yes. We’ve had a few people talking about this and we’re trying to get a way to integrate this as an option. They do do a lot of specialised, customised parts for cars, like accessories to make things easier for people. There’s an extension on the brake pad or extension handles on the wheel, or do different thing. But it’s generally customised to the individual person’s disability. So it’s something we want to have a look at, because the guy that came in to do stuff, he was pretty much doing everything by hand. He was taking moulds of people’s arms and limbs and doing that, then trying to reverse engineer off that. We were like, wow, you could probably nearly 3D scan this and machine stuff that would make this a lot quicker, and then you could just adapt it for each car.
John: Coming back to the core surfboard making, would you see yourself now really more as a curator of the perfect surfboard for individuals?
Sam: I don’t know. You’re always chasing the perfect surfboard! There’s always a compromise somewhere when you make a surfboard. But you learn a lot of different things along the way. We’ve managed to be able to now make quite minute adjustments from one board to the next and we give them to top team riders and they can feel differences in boards. So it makes it great when we’re testing different shapes, different things, trying to get something right. So you can always go back to the version 3, version 4 and go, okay, we like this bit, we like that bit out of this board, and then we start combining them together. So it does give us that option.
John: I think people’s minds will be blown to think that there’s a robot at work in a surfboard factory in the back blocks of Cronulla. But you must be looking at that and starting to think about how other businesses could be using robotics and AI. Is this something that because you’ve done it yourself, do you look around and go, wow, I can see different ways in which this might become pretty much the norm?
Sam: Yes, for sure. We get a lot of people walk into our factory and then you walk into the back corner of it and there’s this giant robot, they’re like, wow! Then the first thing they say to me is, that’s going to steal your job. I’m like, well no, it’s something that actually enhances my job and probably makes it more viable. If I was still here by hand, I probably wouldn’t be able to produce as many boards that we would need to keep going. We’d cut all our margins down. We probably wouldn’t be here. We would’ve been outdone by overseas competitors bringing in massive amount of boards.
John: So as you walk around the community and other businesses, are there other applications that you think are inevitable for robots?
Sam: You see other manufacturing businesses and you go, that’s quite a dangerous situation for an OH&S point of view. You could actually set that task up, say a welding operation, you could actually have a robot weld someone in a process, rather than have someone do it by hand. That would eliminate some of your dangers of having a welder and having all that set up in your workplace and the way everything runs. I know a guy that was welding muffler tips, he was in there, he’d set it up on a jig and would do it by hand and move it along to the next station and he’d do the next part. But he could actually have it there, have a program, and all it basically had to do was follow a circle. He could load the thing up, press a button, does that, pulls it out and goes to the next one. He hasn’t got the physical contact in there. Also, dusty operations, picking and packing operations, you can actually automate it and get a fairly easy process down the line that would help a lot of small businesses, where the cost isn’t too prohibitive.
John: Do you find people are freaked out by the concept? I mean it must make for good dinner party conversation!
Sam: You sort of get people come in and say, this technology and these things are going to take over the world and it’s just going to happen. You’re like, I know how much work we’ve put in to get a robot to get to this point. I’m like there’s a big step to go forward, but you can actually get it to do little things and help make things, so it helps you out. So yes, you see people go, why would you do that, that’s going to take everything away from you. And you’re like, no, it’s making things better. You can actually remain competitive in those situations.
John: Finally, Sam, what advice would you have for businesses looking to innovate around their customers in terms of the incorporation of technology? What would you say to anyone who was thinking I’ve got to try and find a new way?
Sam: Don’t be scared to try something different. You can fit robots into a normal workplace. You could probably have it there making a coffee. I’ve seen one lately that’s flipping burgers, and various small parts in things. It also brings a lot of people into the shop. We have kids coming in all the time and it brings new people into the business, because they’ve heard about it and they want to see it and they’re, wow, we haven’t seen this before; this is really cool. A lot of kids don’t see a lot of manufacturing these days and a lot of things that are happening. But then they see a robot and they go, I’ve seen that on TV, that’s cool, now I’ve actually seen one in real life. We get kids come in here that are like three or four with their parents and then they see the robot move, and then they freak out and get scared. Then the next time they’re coming in going, I want to see the robot again, I want to see the robot again! So it’s like something that brings people into the business. It’s something that helps the business along the way. So it’s definitely interesting!
John: Fantastic. Sam, thanks so much.